Quality Consulting Services we offer at JTA
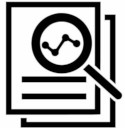
If you would like to become certified to ISO 9001:2015 and/or AS9100D, or you would just like to maintain your current quality management system we are here to do that.
- We can come in and perform a gap audit to give you an idea of where you are and where you need to be.
- Together we will develop a quality plan along an agreed upon timeline, and negotiable pricing. Typically we will write up an informal contract that can be modified as conditions change.
- From here we begin work designing and customizing your quality management system to support internal requirements, to meet the requirements of regulatory bodies, customer quality requirements and the requirements of all stakeholders defined by the system.
- We schedule the audit date while we are developing the quality management system, and compiling records.
- We can send out confirmation to customers who may be expecting the certification to meet their requirements.
- If you are getting certified for the first time, we will then go through the audit to attain your certification. First time certifications can be more rigorous, so the preparation work must be thorough.
- After initial certification, you cut back some of the padding you had to add in to get yourself through initial certification. Now is the time to make the processes more efficient, and to focus on areas that may need work
- About 2 years after your initial audit you should begin to see stable upper and lower limits on your key process indicator (KPI) metrics.
To get the quality system up and functioning well, these are the areas we will support:
